Les étapes CLéS
GO4ZERO va au-delà de la pérennisation des capacités de production cimentière locales d'Holcim sur les marchés du Benelux et du nord de la France. Son objectif est de contribuer de manière significative à la décarbonation de l'industrie de la construction belge sur ces marchés.
Au cœur du projet se trouve la cimenterie d'Obourg (Mons), un site historique où l'activité cimentière perdure depuis plus de 110 ans. Le projet se déroule en deux phases, la première ayant déjà débuté en janvier 2024 et devant se terminer vers 2027, tandis que la seconde devrait s'achever d'ici 2029.
Ce projet, porté par Holcim Belgique, nécessite des investissements dans de nouvelles infrastructures intégrant des technologies innovantes, avec le soutien d'experts dans leurs domaines respectifs, afin de garantir des performances opérationnelles, économiques et environnementales exceptionnelles.
Phase 1 :
GO4ZERO entreprend une première phase ambitieuse de modernisation de son usine existante en adoptant un nouveau processus de production de clinker en "voie sèche". Actuellement, la production de clinker utilise un procédé en "voie humide" avec de la craie, mais elle va basculer entièrement vers le calcaire, une matière moins chargée en eau, provenant de nos gisements situés en rive gauche et en rive droite de l’Escaut, à cheval sur les communes d’Antoing et Tournai.
Le calcaire, riche en carbonate de calcium, sera extrait et traité à Vaulx (Tournai), puis transporté par train jusqu'à Obourg. Les opérations de raccordement et de jonction de voie ont déjà été réalisées dans le Tournaisis, à Vaulx plus précisément, et seront terminées d'ici l'été 2024 sur Obourg.Un investissement de plus de 50 millions d'euros est alloué aux carrières pour le concassage du calcaire, son transfert vers la zone de stockage intermédiaire et son chargement dans des trains.
L'adoption du calcaire comme matière première et l'efficience du nouveau processus en 'voie sèche' vont diminuer la consommation d'énergie thermique de 40% par rapport à la méthode en 'voie humide' actuellement employée. Cette réduction combinée à un choix optimisé de matières premières déjà décarbonées et à un mix de combustibles favorisant la biomasse entraînera une réduction de 30 % des émissions spécifiques de CO2 par tonne de clinker, permettant de se situer en-dessous du futur benchmark européen fixé à 684 kgCO2/tonne clinker en 2026.
L'initiative de GO4ZERO marque une avancée majeure vers une production de clinker plus éco-responsable. Cette première phase, débutée en janvier 2024 pour une durée de 36 mois, a reçu un permis sans aucune réclamation, soulignant ainsi la robustesse et l'adhésion de ce projet.
En parallèle, des investissements importants sont prévus pour l'autoproduction énergétique, notamment avec la construction d'une ferme photovoltaïque flottante et l'intégration d'un système de récupération de chaleur sur le site d'Obourg.
De plus, de nouvelles technologies numériques seront intégrées pour optimiser les performances de l'usine. La production de la première tonne de clinker est prévue pour le début de l’année 2027, représentant un investissement global de 385 millions d’euros.
Vidéothèque
Phase 2 :
La seconde phase du projet GO4ZERO, dont la mise en service est planifiée pour le dernier trimestre de 2028, comprend l’installation d’équipements complémentaires pour permettre le passage à l’oxycombustion, dans lequel l’oxygène remplace l’air ambiant comme comburant. Ce procédé innovant, en partenariat avec la société Air Liquide, permet une concentration du CO2 dans les effluents gazeux à plus de 80 %, contre 30 % lors de la première phase.
Cette transformation nécessite la mise en place d'une chaîne de valeur du carbone complète incluant:
- La capture et la purification du CO2 à plus de 99 %. Cette opération se déroulera au sein d’une entité de purification du CO2 (“Carbon Capture Unit” ou encore “CPU”), qui sera conçue, construite et opérée par notre partenaire Air Liquide sur une parcelle de près d’un hectare au sein de notre usine. Air Liquide est co-bénéficiaire aux côtés de Holcim de l’aide financière de l’innovation Fund et mettra en œuvre sa technologie propriétaire de purification par cryogénie Cryocap Oxy. Les travaux associés démarreront dès l’obtention des permis début 2025 et sont en ligne avec les délais annoncés par les différents acteurs de la chaîne de valeur.
- Le transport du CO2 sous forme gazeuse via pipeline depuis la CPU jusqu'au terminal. Le cadre légal est en cours de définition au niveau des exécutifs wallon et flamand. Il est fortement probable que Fluxys gère ce réseau qui sera composé pour partie du réseau de gaz naturel reconditionné pour le transport de CO2 (principalement jusqu’à Gand) et pour partie de nouveaux pipelines dédiés.
- La liquéfaction et le stockage du CO2 dans un terminal maritime, équipés de systèmes de chargement de bateaux. Plusieurs terminaux à Gand, Zeebruges et Anvers sont en développement, avec Antwerp@C comme projet le plus avancé, dont la construction est prévue pour débuter en 2024 et la mise en opération prévue pour début 2028 au plus tard.
- Le transport maritime du CO2 liquéfié par navire spécialisé, entre le terminal et le hub de séquestration en mer du Nord. Des sociétés spécialisées dans le transport de gaz liquéfié sont en train d’adapter leur flotte aux besoins futurs de transport de CO2.
Le hub de séquestration. Il en existe plusieurs types qui peuvent recevoir le CO2 sous pression afin de l’y stocker de façon durable :
- Des anciennes poches de gaz naturel on-shore (Danemark, Islande) ou off-shore (Pays-Bas, Royaume-Uni, Norvège, Danemark).
- Des aquifères salins profonds.
Les principaux acteurs de l'industrie pétrolière et gazière, tels que Equinor, TotalEnergies, Wintershall Dea et Shell, dominent cette étape de la chaîne de valeur. On y trouve également des entreprises désireuses de contribuer à la chaîne de valeur du carbone, en proposant des solutions intégrées englobant plusieurs de ses éléments.
L’ensemble de cette chaîne de valeur, depuis les carrières jusqu’aux puits de séquestration en Mer du Nord, repose sur des sociétés spécialisées et reconnues pour leur expertise, garantissant la robustesse de l’ensemble du processus.
Cette deuxième phase positionne Holcim Belgique en tête des initiatives pour créer de nouveaux écosystèmes favorisant la valorisation du CO2 et l'économie circulaire.
FAQ
- Les réserves de craie d’Obourg seront épuisées d’ici 2034. Mais nous disposons d’importantes réserves de calcaire dans le Tournaisis. Leurs caractéristiques physico-chimiques, et en particulier leur très faible teneur en eau, permettent un changement du procédé de production de clinker vers la “voie sèche” (au lieu de l’actuelle “voie humide”). Pour rappel, le clinker est le constituant principal du ciment, que nous commercialisons et que nous utilisons pour la fabrication des bétons.
- Ce nouveau four, couplé à la fourniture de calcaire depuis Tournai-Antoing, permettra par son procédé et grâce à la faible teneur en eau de ses matières premières, d’importantes économies de combustibles. Nous projetons une réduction de près de 40% de la consommation thermique du four et autant de CO2 en moins à la clé, par tonne de clinker produite. Vu l’augmentation du cours du CO2 sur le marché fermé européen ETS (quotas d’émission) et l’inflation galopante des coûts énergétiques, construire un nouveau four est indispensable pour maîtriser nos coûts de production et résister ainsi à la concurrence internationale.
- Nous anticipons aussi un renforcement prochain de la réglementation environnementale sur les rejets atmosphériques industriels. Cette nouvelle réglementation demande des investissements importants : ils n’ont de sens que dans une perspective de long terme, pour un nouvel équipement et un nouveau procédé.
- Enfin, ce nouveau four ouvre la voie à de nouveaux développements techniques pour améliorer la performance environnementale. En particulier, l’utilisation d’oxygène pur (plutôt que l’air ambiant) est nécessaire pour mettre en œuvre, à l’avenir, des techniques de capture du CO2.
- Nous avons choisi de construire ce nouveau four sur le site d’Obourg. Cela nous permet en effet de réutiliser et de valoriser une partie des infrastructures existantes.
- Le nouveau four ‘GO4ZERO’ sera construit à l’emplacement de l’actuel stock de laitier. Il sera donc 150m plus proche des habitations que la cheminée actuelle. Nous veillons soigneusement à réduire drastiquement les impacts sonores, visuels et olfactifs dans le design des installations non seulement pour ne pas engendrer de nuisances supplémentaires pour nos riverains, mais également pour limiter encore plus l’impact de nos activités.
- Nous travaillons avec des bureaux d’études spécialisés afin de réduire toutes les sources potentielles de nuisances, à la source : choix des machines, localisation adaptée des sources de bruit, bardages isolants acoustiquement, traitements des effluents gazeux et confinement des installations de stockage ou de déchargement des correctifs et combustibles alternatifs liquides et solides… Rien n’est laissé au hasard.
- Le nouveau four remplace les deux anciens fours, pour une capacité de production équivalente à la capacité actuelle. La mise en œuvre de nouvelles technologies ainsi que le stockage dans des bâtiments fermés des matières premières augmentent cependant le volume construit. En particulier, la tour de préchauffage aura des dimensions certes imposantes, inhérentes au procédé “voie sèche” et au dimensionnement des équipements associés afin de réduire la consommation thermique globale du four et permettre une combustion efficace.
- La tour aura une hauteur approximative de 140 mètres (le design est encore en cours de finalisation, du fait qu’il s’agit d’un tout nouveau concept de combustion). Elle abrite les équipements permettant la décarbonatation de la matière, le précalcinateur. Celui-ci constitue la première partie du nouveau four à clinker et est composé d’une succession de cyclones, des échangeurs de chaleur statiques permettant de préchauffer la matière première (que l’on appelle le cru) et la décarbonater à plus de 850°C. La matière, séparée de son CO2, rentre ensuite dans la seconde partie du four, rotative et légèrement inclinée cette fois, où le cru sera porté à plus de 1450°C pour en permettre la clinkérisation. La tour de préchauffage est inhérente au processus de clinkérisation en voie sèche.
- La cheminée longe cette tour et la dépasse légèrement. Une hauteur importante, combinée à une vitesse de d’éjection des gaz élevée permet une dispersion atmosphérique encore plus efficace
- Aujourd’hui, les fumées sortant de la cheminée sont en grande partie composées de vapeur d’eau et de CO2. La vapeur d’eau se condense en fonction des conditions météorologiques et on voit apparaître le plus souvent un panache blanchâtre, dont la couleur, plus ou moins claire, est principalement influencée par l’orientation du soleil. L’utilisation du nouveau four en voie sèche, du fait de la quantité très limitée d’eau dans les matières premières, aura donc un panache de vapeur nettement moins visible.
- Outre la vapeur d’eau et le CO2, nous retrouverons toujours les mêmes composants dans nos rejets à la cheminée, provenant majoritairement de la combustion inévitable dans un processus de clinkérisation. Cependant, de nouveaux équipements intégrant les dernières technologies disponibles sur le marché, seront installés afin de réduire significativement la présence de ces éléments polluants, améliorant encore sensiblement les performances actuelles.
- - Enfin, la hauteur de cheminée du projet GO4ZERO étant supérieure à celle d’aujourd’hui, elle permettra une meilleure dispersion atmosphérique.
- Pour assurer l’alimentation du nouveau four, nous devons recevoir environ 65 000 tonnes de calcaire par semaine depuis nos carrières du Tournaisis. Cela implique une moyenne de 30 à 32 trains de 2200 tonnes utiles par semaine, qui entreront et sortiront du site d’Obourg. Ce dernier sera aménagé afin de permettre ce flux en toute sécurité et en utilisant les techniques les plus récentes en matière de réduction du bruit et les contraintes opérationnelles les plus limitées possibles.
- Les opérations de déchargement doivent pouvoir être exécutées à toute heure du jour et de la nuit, bien qu’Infrabel nous garantisse a priori un nombre suffisant de sillons pour opérer entre 6h et 24h dans les conditions de fonctionnement actuelles. Les trains de nuit seront donc complémentaires et utilisés en dernier recours, en fonction des aléas de circulation rencontrés en cours de journée.
- Les risques de nuisances sonores sont principalement liés à l’opération de déchargement des trains, à plus de 2000 tonnes par heure. En effet, la locomotive de manœuvre sur site sera un robot électrique, dont les moteurs par nature ne produisent quasiment aucune nuisance. Nous envisageons aussi de pouvoir utiliser des locomotrices duales électricité (sur le réseau Infrabel) et batterie (sur site propre non électrifié), avec un fonctionnement à très faibles vitesses et sans à-coups ni freinage puissant. Nous sommes capables, par une conception adéquate des appareils de voie, de la pose des voies sur notre site et des installations automatisées de déchargement, de limiter les nuisances sonores de nos activités ferroviaires. En particulier pour le déchargement, celui-ci se fera dans une fosse réalisée en béton et située à l’intérieur d’un bâtiment dont la conception a été étudiée afin d’intégrer les meilleures solutions d’isolation acoustique possibles.
- Point positif pour nos voisins d’Obourg, l’exploitation de la carrière de craie - et ses nuisances éventuelles, bien que sous contrôle - prendra fin une fois le nouveau four pleinement opérationnel.
- La disposition des principaux équipements qui ont une puissance acoustique importante a été étudiée afin de trouver le meilleur compromis entre la réduction de la dispersion du bruit vers les voisins les plus exposés et l’optimisation du procédé de production. Nous avons dès le départ prévu des techniques d’isolation phonique des bâtiments dans les cahiers des charges afin de réduire le bruit à la source.
- Des modèles de dispersion acoustique ont été réalisés dans le cadre de l’étude d’incidences. Nous tenons compte des recommandations du bureau d’études afin de réduire notre impact dans l’environnement. En particulier, un soin est apporté aux opérations de déchargement des matériaux dès l’entrée des trains sur site, par un choix judicieux des techniques d’appareils de voie eti de pose de voies, en profitant de l’expérience des acousticiens d’Infrabel, mais aussi par la conception du bâtiment où le déchargement sera effectué. Ce dernier sera bien évidemment fortement insonorisé par un choix judicieux des techniques de construction et des prescriptions sur les matériaux d’isolation et leur épaisseur.
- Le choix des équipements de roulage intègre également la dimension “bruits” : préférence pour des locotracteurs électriques / sur batterie, robots automatisés sur batterie pour les manipulations sur site, fonctionnement à très faibles vitesses sans à-coups, ....
- Le transport du calcaire de Vaulx vers obourg par voie ferrée produira des émissions de CO2 de l’ordre de 5000 t par an.
- Ce projet vise à pérenniser l’activité du site et donc l’emploi pour les 60-70 prochaines années.
- Ce projet a également le potentiel de générer de l’activité supplémentaire: d’une part par la construction du nouveau four et, d’autre part, par la captation et le traitement du CO2, qui sont des métiers d’avenir avec beaucoup de perspectives.
- Des initiatives complémentaires seront prises en matière de formation, pour accompagner le personnel dans l’utilisation des nouvelles technologies.
- La réalisation du chantier lui-même favorise le maintien et même la création de nouveaux emplois dans les entreprises qui participeront à ce chantier historique.
- Les odeurs parfois perçues aujourd’hui sur le site d’Obourg sont liées aux stockages à l’air libre des boues et correctifs. Dans le cadre du projet, les correctifs seront stockés dans un hall à l’entrée du site, les combustibles liquides et solides dans des halls et cuves avec un traitement d’air spécifique approprié. Concernant les boues, il n’y aura plus de stockage temporaire et de pré-traitement, mais uniquement des trémies d’alimentation en direct du four.
- De manière générale, les nuisances olfactives seront totalement maîtrisées avec les nouveaux équipements et mesures prévus dans le cadre de GO4ZERO.
- Avec seulement 5% de camions supplémentaires au grand maximum, l’impact en termes de trafic sera très faible, d’autant plus que la totalité du flux lourd est orienté vers la route industrielle, dédiée au trafic lourd et l’accès par la route d’Obourg, pour le trafic < 3,5T.
- Il faut aussi noter que le Chemin du Pont d’Haine, qui relie la route d’Obourg à la route industrielle en longeant la cimenterie et COMET, sera partiellement privatisé et déclassé dans le cadre de la demande de permis (dossier spécifique avec enquête publique commune), sur toute la longueur de la nouvelle usine, depuis l’entrée de la rue des Fabriques jusqu’au nouvel aménagement réalisé par l’IDEA, près du site de COMET. La route sera d’ailleurs fermée des 2 côtés et les accès sécurisés.
- La procédure de déclassement de voirie et de vieux chemins vicinaux disparus depuis 50 ans sera menée de pair avec la procédure de permis. Le conseil communal montois a avalisé cette demande.
- Des réparations de la route industrielle ont déjà été entreprises mais nous sommes bien conscients que des travaux en profondeur sont nécessaires pour la reconditionner.
- Nous sommes actuellement en discussion avec la ville de Mons sur cette question.
- La route fera partie de l’usine. Les voitures privées rentreront via le Bois Doyen et le pont du chemin de fer et les camions rentreront par la route industrielle. L’usine ne pourra plus être traversée ni par des voitures ni par des camions pour des raisons évidentes de sécurité.
- La possibilité de construire les installations de production de clinker à proximité des gisements de calcaire dans le Tournaisis a évidemment été étudiée mais la proximité immédiate d’habitations et la surface disponible de moins de 30ha auraient entraîné des difficultés supplémentaires de réalisation. Et ce d’autant plus que notre ambition va au-delà du nouveau processus de fabrication de clinker : nous voulons préparer le futur et faire en sorte de devenir neutre en carbone. Cela exigera des équipements qui prennent de la place et les 80ha de terrains dont nous disposons à Obourg nous permettent d’envisager toute une série de solutions industrielles très innovantes et porteuses de nouveaux développements économiques pour notre région. En outre, nous ne souhaitons pas multiplier notre empreinte en développant de nouveaux sites industriels. Au contraire, nous voulons améliorer continuellement nos installations existantes et réutiliser les équipements déjà disponibles et en bon état. Cela nous permettra en développant notre projet sur Obourg de pouvoir faire des économies d’investissement, tout en créant les économies d’échelles plus importantes entre la future unité de production de clinker et les installations de broyage et d’expéditions existantes.
- GO4ZERO c’est notre plan A, c’est une innovation technologique majeure qui constitue sans aucun doute le moyen le plus pertinent de produire demain du clinker en réduisant l’empreinte carbone associée. Il n’existe pas de plan B réaliste et faisable.
- Ce n’est pas encore complètement décidé à ce stade mais des rencontres sont prévues avec le Département Nature et Forêt; nous essayons d’avoir ses recommandations le plus en amont possible.
- Nous avons également l’ambition de constituer des aménagements sur le haut du Bois Doyen de façon à pouvoir limiter au maximum l’impact de la tour sur les quartiers qui seront les plus impactés visuellement.
- La prochaine grande étape est l’obtention du permis unique attendu pour janvier 2023. La construction du four commencera dans la foulée pour une durée supérieure à 3 ans. Les travaux sur les sites de Gaurain/Vaulx se dérouleront en parallèle. La première tonne de clinker en voie sèche est attendue au premier trimestre 2026.
- L’équipe projet se tient à la disposition de quiconque souhaiterait avoir plus d’informations sur le projet, dans l’état actuel de son développement. Nous veillerons à maintenir la page web à jour et à adopter une communication transparente envers nos parties prenantes. Toute question peut être adressée à : GO4ZERO-be@holcim.com.
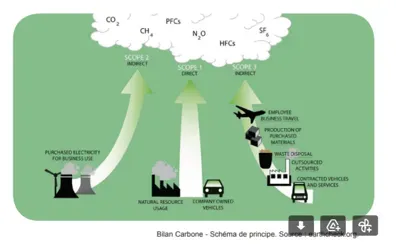
La neutralité carbone d’Holcim en Belgique est définie au regard de ses émissions de CO2 rapportées dans le cadre du système dit ‘ETS’ auquel elle est soumise.
Par ailleurs, Holcim développe des solutions pour réduire son empreinte pour les scopes 2 et 3 dont le niveau est nettement moindre que les émissions directes (scope 1).